摘要: 在某特大桥施工中,其中一座主墩的两个收分面比较缓,采用了“液压滑模+ 大模板倒模法”施工技术进行墩身混凝土浇筑,此法具有施工进度快、安全系数高、操作方便、成本低、外观质量好等特点,可为类似工程提供有益的经验。
关键词: 液压滑模; 倒模法; 混凝土浇筑; 特大桥; 主墩墩身
1· 工程概述
某新建地方铁路特大桥其中一座主墩承台以上墩身高104 m,墩身混凝土工程量为9 003 m3。主墩墩身为单箱单室矩形变截面,顶部箱体厚1. 3 m,底部为高5 m 的实体段,墩身纵桥向宽8m,横桥向顶宽7. 6 m。纵桥向内侧面顶部向下坡度为60∶ 1; 纵桥向外侧面顶部向下坡度为20∶ 1,至墩身19 m 高处向下坡度为10∶ 1。墩身横断面结构见图1。
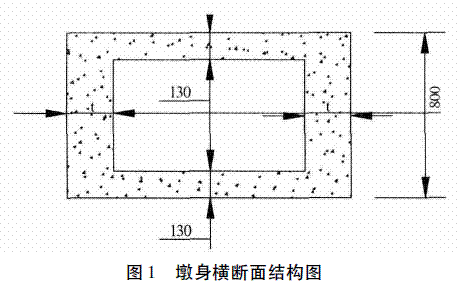
2 ·“液压滑模+ 大模板倒模法”施工方案
2.1 墩身混凝土浇筑施工方案的选取
该桥墩高度大,采用传统手段浇筑有很多不便,安全隐患多,投入人员安装拆除模板工作量大、工期长。同时,因桥墩为两面铅垂、两面收分的结构形式,收分面比较缓( 小于40∶ 1) ,若采用整体液压滑模施工方法,收分面的外观质量无法得到保证且施工难度较大。结合实际情况,选取“液压滑模+ 大模板倒模法”施工方案,可充分发挥铅垂面液压滑模施工的优势,亦可解决较缓收分面的施工问题。
2.2 模板结构体系
模板主要由液压滑升模板和大模板等组成。内模为液压滑升模板,沿纵桥轴线方向分为两部分,中间用收分模板分开。收分模板由小模板制作成可拆卸的结构,小模板外侧设较大模板起固定和封闭作用,当模体收缩一定尺寸后要拆除一小块模板,以保证两端之间有适当的距离。外模两个铅垂面为液压滑升模板,利用开字架连接成整体,形成外滑模体主体模板,铅垂模板宽于混凝土结构面尺寸,紧紧夹着外模的端头模板。端模既是模板,又是铅垂面滑模体的导轨。内模四面均匀安装千斤顶,外模在两个铅垂面安装千斤顶,外模两收分面不安装千斤顶。施工中,采取内、外滑模及大模板之间相对独立的滑升操作方式,滑升时可同步滑升,亦可分次滑升。
3· 墩身混凝土浇筑施工
3.1 施工工艺流程
施工准备→钢筋制安→模板系统安装→预埋件埋设→模板系统初滑→模板系统滑升→混凝土修饰、养护→模板系统拆除。
3.2 模板系统安装
模板系统依据构筑物结构尺寸设计,在场外进行制作并进行组装调试,滑模体现场采用塔吊整体安装。安装时先测量放样弹线用于标明墩身平面位置轮廓线。由于该桥墩底5 m 为实心段,故开始只安装模板系统的外模部分,当实心段和马蹄倒角浇筑完成之后安装模板系统的内模部分。在安装开字架滑模体时,为减小或避免在浇筑过程中仓内混凝土侧压力造成模体下侧外张,应将开字架下端部内空尺寸适当减小( 如5mm) 。
滑模组装检查合格后,安装千斤顶、液压系统,插入支承杆并进行加固,插入的支承杆的起始位置位于墩身箍筋的内侧并对操作平台进行铺板封闭。液压系统的安装由设备提供厂家负责现场指导安装调试。供电采用胶皮电缆线,设照亮、能源启关把持盘,电源零线接地牢靠并设置漏电保护器,备好备用电源。
3.3 模板系统初滑
初滑在模体拼装、钢筋安装验收合格后严格按以下六个步骤进行: 第一次浇筑10 cm 厚细骨料混凝土或砂浆,接着按分层30 cm 浇筑两层,当厚度达70 cm 时,滑升3 ~ 5 cm 检查脱模的混凝土凝固情况,第四层浇筑后滑升15 cm,继续浇筑第五层,滑升15 ~ 20 cm,第六层浇筑后滑升20cm,若无异常情况,便可进行正常浇筑和滑升。
每次提升要根据混凝土入仓时间、速度和混凝土强度等情况确定提升次数和每次提升行程,以免造成出模时混凝土强度偏大、滑升困难。出模时混凝土强度过小,会造成混凝土流坠、跑浆、坍塌; 出模时混凝土强度过高,会造成混凝土出现拉裂、划痕、疏松、不密实、不美观等现象。按照《液压滑动模板施工技术规范》要求,混凝土出模强度宜控制在0. 2 ~ 0. 4 MPa。根据对现场混凝土拌合物成型后1 h、2 h、3 h、4 h、6 h 的强度进行测试可知,正常气温( 20 ℃ ± 2 ℃) 下,3~ 4 h 后混凝土强度可达到0. 25 ~ 0. 41 MPa,此时若用大拇指去摁混凝土表面,表面有轻微痕迹但不下陷,混凝土表面砂浆不沾手,滑升时有“沙沙”的摩擦声。
3.4 模板系统滑升
每次提升前,检查支承杆有无脱空现象,拉钩钢筋与操作平台有无挂连之处。模板要保持清洁,时常刷油,在滑升进程中,及时清理粘结在模板上的砂浆等物。施工进入正常浇筑和滑升时,应尽量保持连续施工,并设专人观察并分析混凝土表面情况,根据现场条件确定合理的滑升速度和分层浇筑厚度。前后二次滑升的时间间隔不宜超过1. 5 h; 因故不能连续提升时,每隔1 ~ 2 h 将千斤顶提升1 ~ 2 个行程,以减小混凝土与模板的粘结。
滑升过程要安排专人检查钢筋安装、模板偏位扭曲、支承杆稳定和出模混凝土质量等情况。在正常滑升阶段,要控制好墩身的垂直度。为保证模体不发生偏移,垂直度偏差应≤0. 3%且≤20mm。
外侧两个收分面根据液压滑升模板的施工进度,及时采取大模板倒模法施工。
3.5 混凝土修饰与养护
混凝土脱模后,由于模板的接缝不平或提升拉裂等情况,其表面可能出现凹凸不平或裂缝等缺陷,需及时进行修补,用抹子抹平,或用混凝土原浆补平压光。混凝土采用洒水养护。
4· 施工质量控制
4.1 钢筋安装控制
钢筋安装不正确对模板的滑升影响很大,钢筋安装时,先将四角的四根钢筋调直,以保证混凝土保护层厚度。在1 ~ 2 m 的高度安装水平箍筋,该水平箍筋须顺直、不弯曲,并保证其它主筋安装好后大面平整,固定好之后再根据钢筋间距安装其它主筋。水平筋、防裂钢筋网的安装不能接触模板,以避免在滑升过程当中增加摩阻力。
4.2 混凝土质量控制
混凝土的凝固时间是滑模施工的关键,初凝时间过早会导致混凝土与模板粘结,需结合现场情况调整、优化配合比,选取合适的初凝时间。浇筑时做到混凝土均匀、对称入仓,避免出模混凝土的强度不均匀等造成质量缺陷。
该桥墩为箱体结构,在混凝土浇筑施工中,箱体内空气流动性较差,造成箱体内、外环境的温差较大,进而会影响内、外侧的混凝土初凝时间,需采取在内侧浇水降温、设置通气孔等措施,以保证混凝土外观质量。
4.3 墩身垂直度控制
( 1) 支承杆的垂直度是影响墩身垂直度的直接原因。为了控制好支承杆的垂直度,支承杆安装时采用水平尺交换90°紧靠在支承杆上观察水准泡是否居中的方式,若不居中则在调整居中后将支承杆顶端固定,滑升过程中要随时检查其垂直度并及时进行调整。
( 2) 滑模系统高程、垂直度、几何尺寸检查验收完毕,在外模两个铅垂面的四个角各安装1 个绞盘,使用直径2 mm 的钢丝绳悬挂1 个垂球( 4个角共4 个锤球) ,每个垂球重10 kg 左右,为减少垂球晃动,将其悬置于水桶或油桶内。模板每滑升一次释放垂球至墩底的桶内,通过钢尺检查垂球线与墩顶、墩底和模板的距离来确定模板的垂直度和墩身的总体垂直度。
( 3) 每天利用全站仪进行高程、结构尺寸量测及校核,并用钢卷尺随时检测各部位结构尺寸情况。
5· 结语
在该桥墩施工过程中,浇筑上升平均速度为2. 6 m/d,施工质量得到了各方一致认可。采用“液压滑模+ 大模板倒模法”施工体现了以下优点,可在类似工程中推广运用。
( 1) 简化了施工工序,缩短了工期,能大大节约施工成本。
简化了立模、拆摸等工序,能使混凝土连续作业,加快了施工进度,明显快于其它现浇方法并缩短了工期。由于结合采用了液压滑模施工技术,节省了大量的墩旁支架、模板和起吊设备的投入,整个模体简单,投入小,大大节约了成本。
( 2) 保证了高墩施工的安全。由于减少了高空安装和拆除模板作业,整个模体装置荷载主要由提升架、支承杆等传至已浇筑的墩身混凝土,从而保证了结构安全稳固以及施工期间的人员安全。
( 3) 大大提高了高墩混凝土施工质量。浇筑过程连续作业,减少了施工缝,加强了混凝土的整体性,提高了混凝土质量。
( 4) 在高墩施工中,为解决有较缓收分面条件下采用液压滑模施工方法提供了新的思路。